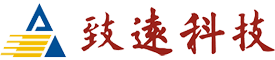
- 简体中文
来源:2016 特种铸造论文集
作者:葛继龙、赵海东、胡启耀、高军民、王卓明
摘要:
铝合金压铸件的表层组织对铸件使用性能有重要的影响。研究不同快压射速度下ADC12铝合金压铸件的表层组织特征,并通过金相和数值模拟进行分析。结果表明,压铸件存在3种不同特征的表层组织:仅含有一层富集致密的初生a Al相;外层为正常的压铸凝固组织(初生a-Al相和共晶相)邻接细小的初生a AI相层;属正常的压铸凝固组织。同时,探讨了快压射速度和型腔位置对表层组织的影响。
压铸件表层组织的形态会影响压铸件的耐压性、气密性、耐蚀性以及后续的机械处理,同时,表层组织的特性也会影响铸件的力学性能。表层和心部组织由于晶粒尺寸及形貌存在差异,具有不同的硬度,表层组织的硬度相对较高,而心部则相对较低。
目前,关于压铸件表层组织的研究主要集中在其形成机理及其与力学性能的关系上,但关于工艺参数对压铸件表层组织的研究目前报道极少。因此,本课题以ADC12铝合金为研究对象,对不同快压射速度下压铸件表层组织的特征进行了观察,并采用Flow 3D软件对压铸件的充型过程进行了数值模拟,分析了表层组织演变规律,旨在为压铸实际生产提供参考。
1 试验方法
试验在TOY0350t压铸机上进行,图1为试验压铸件浇注系统。其中,4根矩形横截面拉伸试样厚度t分别为2、4、6和8 mm,其余尺寸均保持一致,矩形板状试样厚度t为2 mm。采用ADC12铝合金,经ARL4460直读光谱仪检测,其化学成分见表1。压铸工艺参数:浇注温度为650℃,铸造压力为65 MPa,慢压射速度为0.5 m/s。
为了研究压铸工艺对铝合金压铸件的表层组织特征的影响,进行了不同快压射速度(1、2和3 m/s)压铸试验。采用4根拉伸试样进行金相观察分析,取样截面见图1中A、B、C、D。随后,将所取微观分析试样进行研磨、抛光、腐蚀、清洗后,用Leica DMI 5000M光学显微镜观察各截面处表层组织,并采用图像定量分析系统对表层组织厚度进行定量分析。
2 结果与分析
2.1微观组织
图2为不同快压射速度下压铸件截面A、B、C、D处的表层显微组织。可以看出,压铸件的表层组织并不只有单一的类别,图2a、图2b、图2d、图2g、图2h及图2j为相同类别的表层组织,即靠近铸件表面为一层细小的a-Al和Al-Si共晶组织,其组织特征与正常的压铸凝固组织相同。向铸件内部则邻接了一层细小富集的a-Al相;图2e、图2f、图2i、图2k、图21为相同的表层组织,即铸件表面存在一层富集致密的a-Al;图2c中铸件表层区域组织与心部组织无明显区别,同时,可以看出压铸件表层区域均没有出现孔洞。对于表层组织,根据其特征分别以Skin2、Skinl和No Skin命名,并据此对各截面处表层组织进行分类,结果见表2。为进一步研究表层组织的变化规律,对其厚度进行测量统计,结果见表3。
结合表2、表3可知,当快压射速度为1 m/s,各铸件的表层组织均为Skin2,但截面A、C处Skin2的厚度要大于截面B、D处。当快压射速度为2 m/s时,截面B、D处铸件的表层组织为Skinl,而截面A、C处铸件的表层组织则为Skin2,同时,从图2a、图2b和图2g、图2h可以看出,Skin2的厚度相比l m/s时明显减小。当快压射速度为3 m/s时,各铸件的表层组织以Skinl为主,但截面A处并没有明显的表层组织特征出现;从图2e、图2f和图2k、图21可以看出,当快压射速度从2m/s增加至3 m/s时,Skinl的厚度略有减小。
2.2数值模拟
图3为不同快压射速度(1、2、3 m/s)下金属液充填形态的模拟结果,充型完成时间分别为0. 063 02、0. 031 46和0.021 01 s。可以看出,随着快压射速度的增加,金属液充满型腔的时间逐渐缩短,但是金属液在充型过程中的流动形态并未发生明显变化。对于截面A、C而言,金属液在充型过程中的流动方向始终与该处模具表面保持平行,没有发生明显的碰撞:对于截面B、D而言,金属液流入型腔后,先与型腔的一侧接触,当型腔截面积减小时,金属液流动方向发生偏转并与截面B、D处模具表面发生碰撞。图4为不同快压射速度下,金属液在截面B、D处的流动形态和速度。从速度方向可以看出,金属液充填到该位置时.方向发生变化,与模具表面发生明显碰撞。随着快压射速度的增加,金属液的速度显著增加,因此金属液与模具表面的碰撞愈发剧烈。
3 试验结果与分析
3.1 充型速度和凝固压力的影响
压铸充型过程中金属液流动速度很快,如果把高速的金属液看作是高速的液滴,则液滴对模具表面的撞击压力将达到l08数量级。压力增加,液滴与模具表面的热传递随之加快,从而使撞击处的模具表面温度迅速升高。充型过程中金属液会与模具表面发生不同方式的碰撞,因此模具表面温度变化也会有所不同,且碰撞速度越大,模具表面温度升高越多,而模具温度的变化将对金属液的凝固产生重要影响。
在压铸充型结束后,通常要用超过50 MPa的压力作用于正在凝固的金属液上,微观上影响铸件组织成分、形核激活能、扩散激活能、非晶形成能力等,宏观上对金属熔点和平衡相图、宏观铸造缺陷、材料热物理性能和铸件/模具的界面传热等有影响。压力P对金属熔点的影响可根据Clausius-Clapeyron方程确定:
式中,Tm为金属常压下的熔点,K;dTp为压力作用下熔点的变化量,K;V1、Vs分别为金属液相和固相的摩尔体积,m3/mol;Lm为结晶潜热,J/mol。
从式(1)可知,压力的增加会提高纯Al、纯Si的熔点.Al-Si合金共晶温度也随之升高,故平衡相图向上移动;压力会提高Si原子在Al中的固溶度,故共晶成分点和最大固溶点均向右移动。在挤压铸造过程中,压力为69 MPa时,共晶成分点将会从12. 6%提高到16.5%,当压力增加至150 MPa时则会提高到18.7%。因此,若压铸充型结束后,金属液立即在较高的增压压力作用下凝固,铸件表层的a-Al含量将显著提高,而共晶相的含量相应减少。
3.2型腔位置对表层组织的影响
当快压射速度为1 m/s时,金属液流动速度相对缓慢,对模具表面作用力较小,导致金属液与模具表面间的温度梯度较大,在增压压力作用之前金属液便率先发生凝固,从而形成Skin2。由于截面A、B、C、D所在型腔位置不同,金属液在充型过程的流动形态及对模具表面的作用力也有所不同,从而产生不同的温度梯度。根据充型过程的模拟结果可知,截面B、D处金属液与模具表面发生明显碰撞,模具表面温度较高。同时,由于B和D位于型腔内部,金属液充填到该位置时,温度降低较小,导致金属液与模具表面间的温度梯度相对截面A、C较小,因此截面A、C处金属液凝固速度相对较快,先凝固区域的厚度增加,Skin2的厚度相对较大。此外,型腔位置的不同使增压压力传递的效果有所不同。从图2可知,快压射速度为3m/s时,截面A处并没有形成表层组织,可能是增压压力的传递有所衰减导致金属液未在高压下凝固,具体原因仍需要进一步的研究分析。
3.3快压射速度对表层组织的影响
快压射速度的增加使金属液与模具表面之间的碰撞速度增加,使模具表面温度上升,同时,金属液温度降低,故金属液与模具表面之间的温度梯度逐渐减小。当快压射速度为1m/s时,各截面均在表层形成Skin2,当快压射速度增加至2m/s时,对于截面B、D而言,由于温度梯度减小,充型完成后表层金属液并未率先发生凝固,而是直接在增压压力作用下形成Skinl;对于截面A、C而言,金属液与模具表面之间仍然存在较大的温度梯度,表层金属液在增压压力作用前发生凝固并最终形成Skin2,同时,由于温度梯度相对1 m/s时有所减小,金属液的凝固速度减小,Skin2的厚度随之减小。当快压射速度继续增加至3m/s时,金属液与模具表面之间的温度梯度进一步减小,B、C、D截面均形成Skinl,但Skinl的厚度相对于2 m/s时的结果有所减
小。
4 结 论
(1)压铸ADC12铝合金表层组织主要有3种特征:金属液在充型结束未发生凝固时,在增压压力作用下凝固,表层具有初生a-Al相较多而共晶含量较少的组织;当金属液在充型过程发生凝固,外表面为细小的初生a-Al和Al-Si共晶组织,向铸件内部邻接了增压压力下凝固的较多初生a-Al相而共晶相含量较少的组织;正常凝固的初生a-Al和Al-Si共晶组织。
(2)型腔位置的不同使金属液流动形态发生变化,导致金属液与模具表面之间的温度梯度不同。型腔边缘部位产生的温度梯度较大,型腔中间部位产生的温度梯度较小,因此型腔边缘部位表层易形成Skin2,而中间部位则更易形成Skinl;当两部分均形成Skin2时,边缘部位的厚度大于中间部位。
(3)随着快压射速度增加,金属液与模具表面之间的温度梯度逐渐减小,压铸件表层组织发生从Skin2向Skinl的转变,且表层组织的厚度均逐渐减小。