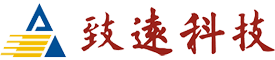
- 简体中文
一、氧化夹渣
缺陷特征:
氧化夹渣多分布在铸件的上表面,在铸型不通气的转角部位。断口多呈灰白色或黄色,经x光透视或在机械加工时发现,也可在碱洗、酸洗或阳极化时发现。
产生原因:
(1)炉料不清洁,回炉料使用量过多。
(2)浇注系统设计不良。
(3)合金液中的熔渣未清除干净。
(4)浇注操作不当,带入夹渣。
(5)精炼变质处理后静置时间不够。
防止方法:
(1)炉料应经过吹砂,回炉料的使用量适当降低。
(2)改进浇注系统设计,提高其挡渣能力。
(3)采用适当的熔剂去渣。
(4)浇注时应当平稳并应注意挡渣。
(5)精炼后浇注前合金液应静置一定时间。
二、气孔、气泡
缺陷特征:
铸件壁内气孔一般呈圆形或椭圆形,具有光滑的表面,一般是发亮的氧化皮,有时呈油黄色。表面气孔、气泡可通过喷砂发现,内部气孔、气泡可通过X光透视或机械加工发现气孔、气泡在X光底片上呈黑色。
产生原因:
(1)浇注合金不平稳,卷入气体。
(2)型(芯)砂中混入有机杂质(如煤屑、草根等)。
(3)铸型和砂芯通气不良。
(4)冷铁表面有缩孔。
(5)浇注系统设计不良。
防止方法:
(1)正确掌握浇注速度,避免卷入气体。
(2)型(芯)砂中不得混入有机杂质以减少造型材料的发气量。
(3)改善(芯)砂的排气能力。
(4)正确选用及处理冷铁。
(5)改进浇注系统设计。
三、缩松
缺陷特征:
铝铸件缩松一般产生在内浇道附近非冒口根部厚大部位,壁的厚薄转接处和具有大平面的薄壁处。在铸态时断口为灰色, 浅黄色经热处理后为灰白浅黄或灰黑色在x光底片上呈云雾状严重的呈丝状缩松,可通过X射线、荧光低倍断口等检查方法发现。
产生原因:
(1)冒口补缩作用差。
(2)炉料含气量太多。
(3)内浇道附近过热。
(4)砂型水分过多,砂芯未烘干。
(5)合金晶粒粗大。
(6)铸件在铸型中的位置不当。
(7)浇注温度过高,浇注速度太快。
防止方法:
(1)从冒口补浇金属液,改进冒口设计。
(2)炉料应清洁无腐蚀。
(3)铸件缩松处设置冒口,安放冷铁或冷铁与冒口联用。
(4)控制型砂水分和砂芯干燥。
(5)采取细化晶粒的措施。
(6)改进铸件在铸型中的位置,降低浇注温度和浇注速度。
四、裂纹
缺陷特征:
铸造裂纹:沿晶界发展,常伴有偏析,是一种在较高温度下形成的裂纹在体积收缩较大的合金和形状较复杂的铸件容易出现。
热处理裂纹:由于热处理过烧或过热引起,常呈穿晶裂纹。常在产生应力和热膨张系数较大的合金冷却过剧。或存在其他冶金缺陷时产生。
产生原因:
(1)铸件结构设计不合理,有尖角,壁的厚薄变化过于悬殊。
(2)砂型(芯)退让性不良。
(3)铸型局部过热。
(4)浇注温度过高。
(5)自铸型中取出铸件过早。
(6)热处理过热或过烧,冷却速度过激。
防止方法:
(1)改进铸件结构设计,避免尖角,壁厚力求均匀,圆滑过渡。
(2)采取增大砂型(芯)退让性的措施。
(3)保证铸件各部分同时凝固或顺序凝固,改进浇注系统设计。
(4)适当降低浇注温度。
(5)控制铸型冷却出型时间。
(6)铸件变形时采用热校正法。
(7)正确控制热处理温度,降低淬火冷却速度。
五、缩孔
产生原因:
金属液有液态转为固态时,体积变小(收缩)。若无金属液补充,便会形成缩孔。通常发生在较慢的凝固处。
防止方法:
(1)增加压力。
(2)改变模具温度。局部冷却、喷脱模剂,降低温度。有时只能改变缩孔位置,而非消除缩孔。
六、脱皮
产生原因:
(1)充填模式不良,造成金属液重叠。
(2)模具变形,造成金属液重叠。
(3)夹杂氧化膜。
防止方法:
(1)提早切换为高速。
(2)缩短充填时间。
(3)改变充填模式,浇口位置,浇口速度。
(4)检查模具强度是否足够。
(5)检查销模装置是否良好。
(6)检查是否夹杂氧化膜。
七、空蚀
产生原因:因压力突然变小,使金属液中的气体忽然膨胀,冲击模具,造成模具损伤。
防止方法:避免浇道截面面积的急速变化。