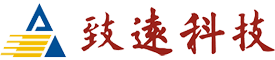
- 简体中文
陈学美,朱仁举
卡斯马汽车系统(上海)有限公司,上海201814
摘要:根据真空压铸的原理及优势,指出了高真空压铸技术开发的主要内容;高真空压铸技术在传统铝合金压铸汽车配技术革新、铝合金副车架、新能源电池壳体及汽车铝合金结构件的应用。提出高真空压铸技术的未来发展方向。
关键词:真空压铸;真空阀;喷涂;压铸模具
在欧洲,从1994年AudiA8轿车的全铝合金立体构架开始,高真空压铸技术的应用领域得到了切实的扩展,技术本身也获得持续发展,对汽车轻量化及改善燃油经济性作出了积极的贡献。从2010 年以后,国内几大汽车零配件厂陆续引进了真空压铸技术,2014年首批件进入量产阶段。
1真空压铸
1. 1原理
真空压铸技术是在传统压力铸造技术的基础上辅以对型腔抽真空技术,即先采用真空抽取装置将压铸模内压室和型腔内的气体抽出,使金属熔体在相对真空的条件下充填型腔。在压铸过程中利用真空压铸技术抽出压铸模内压室和型腔内的气体,能消除或显著减少压铸件内的溶解气体和气孔, 提高铸件内部组织致密度,从而达到提升压铸件的表面质量和综合力学性能的目的。
高真空压铸技术主要有方法,一是德国Muller-Weingarten公司和VAW公司联合研发的Vacural法, 二是德国Alcan-BDW公司推出的MFT法,又称High-Q-Casting。
Vacural法的工作原理,它是将熔化炉通过升液管和压射室直接相连,当模具合模时,模具型腔、 压射室及升液管形成一个封闭的空腔;抽真空开启,将金属液吸入到压射室内进行定量,冲头开始起低速,封闭压射室上的进料口,继续抽真空,直至冲头起高速前型腔达到设定的真空度后关闭真空,冲头进行高速压射成型。
MFT的工作原理,当模具合模时,铝液定量后通过导流槽进入到压射室内,冲头起低速封闭浇料口后设备开始抽真空,待冲头起高速,充填至型腔2/3时关闭真空完成压射成型。其工艺特点是采用多浇道和大截面积内浇口,以保证金属铝液在极短时间内填充满型腔。MFT的优势在于应用到普通压铸机上,真空阀本身的重复生产性高、反应时间稳定、能对每个铸造循环实施监控、可在动模或者定模多重真空系统上加以扩展以及易于保养;型腔的真空度可达到20-50mbar.
1.2真空压铸优点
真空压铸生产的铸件具有以下优点:
压铸件可进行热处理;
压铸件具有良好的焊接性;
降低了铸件内部的气孔率,使铸件内部组织致密,提高了压铸件的机械性能;
改善了充型条件,能够生产壁厚薄,结构较大的铸件;
真空度的存在,减小了型腔内的反压力,压射比压可以降低,有利于延长压铸模具寿命。
2高真空压铸技术开发
2.1铝液的熔炼
铝合金液质量优劣会严重影响到铸件质量,合金的化学成分、杂质含量、含气量及含渣量等都 会影响铸件的力学性能。熔炼的合金锭与回炉料的比例需要严格控制,回炉料需要进行清洁及烘干处理。熔炼的温度控制在670〜760°C以内,过高易发生氧化吸气,过低温度不易分离夹渣且影响熔化效率。
铝合金液的净化按照机理可以分为吸附精炼和非吸附精炼。其中吸附精炼依靠精炼剂产生吸附 氧化夹杂及其表面依附的氢气,达到净化铝液目的。而依靠其它物理作用的精炼方法统一称为非吸附精炼。
目前最为常用的精炼方法是采用氮气(或氩气)通过除气机的旋转头吹入到铝液中,精炼过程 需要控制铝液的温度、气体流量、除气机的转速、除气机旋转头插入铝液的深度及除气精炼的时间。
2. 2真空阀的选用
真空阀是真空压铸的一个核心,目前真空阀有机械式结构、液压式电磁控制阀结构及冷却排气片结构。
机械阀的工作原理是利用合金液的动能在最后充型点将机械阀关闭。
液压式电磁控制阀工作原理是阀镶嵌到压铸模具中,其优点排气能力大,抗污染能力强;缺点 是需要电磁控制及液压源,关闭响应时间受电磁阀影响。且对压铸单元控制系统要求高,阀的工作 过程受压铸设备控制。
冷却排气块按照结构又分为平面排气片和立体排气片,其中立体排气片“开思特”三维搓衣板较 平面排气片具有更大的抽气通道截面积,提高抽气效率。按照冷却方式又分为水冷式和自冷式,其中水冷式通常采用热作模具钢加冷却水通道;自冷式的原理是靠自身传导热量来将排气块中的合金液冷却,铍铜合金是最适合的制作材料。
选择何种真空阀,取决于设备接口及对铸件质量的要求。
2.3喷涂技术
压铸模具的喷涂的主要作用是在模具表面形成保护膜,降低铸件与模具之间的粘附力,使铸件从模具中顺利脱模;减少铸件与模具成型部位的摩擦;且对模具表面进行冷却,使模具温度保持平衡。针对不同模具型腔,设计相应的成型喷涂头,选择合适的脱模剂,确保型腔各个部位能够得到 被有效均衡喷涂。
2.4压铸模具
2.4.1压铸模具设计
确定好分型面,选择内浇口位置,布置好内浇口后进行横浇道及直浇道设计,并确定冲头尺寸。再进行溢流渣包设计,确定真空阀数量,完成排溢系统设计。
进行模具成形零件、顶出系统及模具温控系统设计。
模具密封系统设计,高真空压铸技术的关键是要能确保模具型腔内的真空度,模具的密封效果尤为重要。一般模具需要在模具分型面及模仁镶块拼接处均设置密封,且要确保顶杆镶针等孔的配合精度,减小漏气部位,保证模具的密封性。
2.4.2压铸模具制作
根据模具的结构,选择合适的模仁材料,确定模具的热处理工艺及表面处理方法。
2.5铸件热处理
真空压铸件的热处理主要以T7及T5为主,压铸件的装炉方式,需要根据不同的铸件结构设计特定的料架,尤其是壳体类或结构件类铸件,其尺寸大,形状复杂,容易在热处理过程中导致铸件变形。
3真空压铸在汽车配件上的应用
3.1传统压铸汽车配件技术革新
汽车发动机铸件,如缸体、缸盖罩、链轮壳、油底壳等,多属于形状复杂、结构多变、尺寸精 密和致密性高的铸件,由于高标准、高成品率的要求,对铝合金铸造工艺、品质保证等提出了挑战 [5]。这类件也通过技术革新引进了真空压铸工艺。将传统的排气通道改为真空抽气结构,以提高铸件的内部质量。
3. 2铝合金副车架
副车架可以看成是前后车桥的骨架,是前后车桥的组成部分。其功能是阻隔振动和减少噪声直 接进入车厢。原铝合金副车架一般采用重力铸造、低压铸造或差压铸造。此类铸件壁厚相对较厚, 壁厚在3〜5mm之间,因安装需求有较多厚大的安装凸台及橡胶减震安装孔。为提高铸件生产效率, 铸件结构由原中空结构改为单面或者双面加强筋结构,并将真空压铸工艺引用到此类铸件的生产。
3. 3新能源电动车电池壳体
铝合金电池壳体伴随着新能源电动车同步开发出来,因其使用工况,要求壳体具有较高的机械 性能及延伸率,同时也有内部质量及气密性要求。此类铸件的壁厚一般只有3.0-4.5mm间,长宽尺寸一般在600-1000mm之间。此种结构普通压铸工艺无法达到要求,就需要采用真空压铸或高真空压铸才能满足铸件的质量要求。
3.4车身结构件
汽车结构件指的是汽车中的承载件或受力件,与汽车安全性密切相关。在汽车车身中,许多结构件装在车身结构的节点上并与其他构件连接形成抗变形的高强度框架,这类结构件通常具有尺寸大、壁薄、结构复杂等特征。由于在行驶中要保证汽车可靠的安全性,所以对汽车结构件的力学性 能要求高。此类件因与其它车身件的装配联接方式通常采用焊接或者铆接,这就要求此类件且有 较高的延伸率及焊接性。常规压铸工艺生产的铸件无法满足此类要求,需要采用高真空压铸工艺。
车身结构件主要有前轮罩、后轮罩、纵梁、B柱、横梁、车门框等。壁厚通常为2.0-3.0之间, 以2.5mm壁厚较多,铸件具有尺寸太,壁厚薄,加强筋多的特征。结构件的开发,将高真空压铸工艺引入到大批量生产阶段。
4高真空压铸技术发展方向
4.1微量喷涂技术
现使用的水基脱模剂,在喷涂后需要进行吹干,整个喷涂过程占压射循环的1/4左右。其喷涂 量大,给废水处理、环境保护及资源带来了压力。如何减少每次喷涂量,缩短喷涂时间,提高生产效率。这个要求改进喷涂系统及脱模剂,调整喷涂工艺方面作研究及生产验证。
4. 2髙性能的铸态铝合金材料
应对汽车结构件机械性能的要求,对高性能的铸态铝合金材料尤为迫切。通过添加合金元素来 提高真空压铸件的铸态性能。减少或省略热处理工序,对高真空压铸工艺经济性有重要意义。
4. 3模具温控系统及监控
随着微量喷涂技术的推广,这对模具的温控系统提出了更高的要求。原通过喷涂带走的热量需要通过模具的温控系统传导出去。如何设计好模具各个部位的冷却通道,选择好何种模温机,如何控制模具各区域温度,采用模温精确控制系统尤为重要。
4.4提髙压铸模具寿命
压铸模具主要失效形式有热裂、整体脆断、侵蚀或冲刷等,其中以整体脆断最为严重。如何提 高压铸模具寿命需要从压铸模具设计、模具材料、热处理、模具加工及使用维护综合考虑。
5结语
高真空压铸技术的推广,使得压铸工艺水平又达到了一个新的高度,扩大了压铸工艺的应用范 围。与其工艺相匹配的技术也随市场需求应运而生。