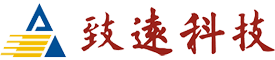
- 简体中文
铸造是国民经济重要的基础工业之一,但铸造 过程的控制、设计及工艺流程往往依赖于经验判断, 因而铸件的质量不易保证,废品率较高。压力铸造 是特种铸造的一种,其实质是液态或者半液态金属 在高压力作用下,以较高的速度充填型腔,并在压力 作用下凝固而获得铸件的一种方法。要获得高质 量、高水平压铸件,使压铸件达到光洁、轮廓清晰、组 织致密、强度高的要求,需要对压铸过程中各影响因 素进行协调统一。对于铝合金压铸件,从生产准备 到批量生产,牵涉的环节很多,影响因素也很多,包 括材质、模具、设备、工艺等各方面。
1 压铸铝合金的分类及性能
压铸铝合金有良好的使用性能和工艺性能,因 此铝合金的压铸发展迅速,在各个工业部门中得到 广泛的应用,用量远远高于其他有色合金,在压铸生 产中占有极其重要的地位。按所含基本元素可将铸造铝合金分为Al-Si合金、Al-Cu合金、Al-Mg 合 金、Al-Zn合金。
1. 1 Al-Si合金
由于共晶Al-Si合金具有结晶温度间隔小、合 金中硅相有很大的凝固潜热和较大的比热容、其线 收缩系数也比较小的特点,因此其铸造性能一般要 比其他铝合金的好,其充型性能也好,热裂、缩松倾 向比较小。Al-Si共晶体中所含的脆性相(硅相) 数量最少,质量分数仅为 10% 左右,因而其塑性比 其他铝合金好,组织中仅存的脆性相还可通过变质 处理降低其脆性。实验表明Al-Si共晶体在其凝 固点附近温度仍保持良好的塑性,这是其他铝合金 所没有的。
铸造合金组织中常要有相当数量的共晶体,以 保证其良好的铸造性能;共晶体数量的增加又会使 合金变脆而降低力学性能,两者之间存在一定的矛 盾。但是由于Al-Si共晶体有良好的塑性,能较好地兼顾力学性能和铸造性能两方面的要求,所以Al-Si合金是目前应用最为广泛的压铸铝合金。
我国压铸铝合金品种中,绝大多数以Al-Si合 金为主,这类合金存在强度较低、切削性能不够好、 螺纹加工困难等现象,所以近年来我国正在开发高 强度合金。
在美国的高强度Al-Si-Cu合金(SC84A、SC114A、SC84B、SC102A)中铜的质量分数为 2.0% ~4.0%,锌的质量分数不超过3%,硅的质量分数 为7.5% ~12.0%(具体见表1),具有较高的力学性 能、良好的压铸工艺性能和机械加工性能。近年 来我国研究的Al-Si-Cu新型高强度铝合金有 YL112、YL113、YL117 等。
1. 2 Al-Mg合金
Al-Mg合金的性能特点是:室温力学性能好; 抗蚀性强;铸造性能比较差;力学性能的波动和壁厚 效应都比较大;长期使用时,有因时效作用而使合金 的塑性下降,甚至压铸件出现开裂的现象;压铸件产 生应力腐蚀裂纹的倾向也较大等。Al - Mg 合金的 缺点部分抵消了它的优点,使其在应用方面受到一 定的影响。
1. 3 Al-Zn合金
Al-Zn合金压铸件经自然时效后,可获得较高 的力学性能。当其锌质量分数大于10% 时,强度显 著提高。此合金的缺点是耐腐蚀性差,有应力腐蚀 的倾向,压铸时易热裂。常用的Y401合金流动性 好,易充满型腔,缺点是形成气孔的倾向性大,硅、铁 含量较少时,易热裂。
1. 4 特殊性能的压铸铝合金
国内外研制的特殊性能的压铸铝合金有:
装饰型Al-Mn合金:适用于阳极氧化处理和 着色处理,伸长率高,还具有相当的耐蚀性。但其强 度不高,收缩率大,易粘模。
热处理型Al-Si-Cu合金:可进行淬火后不完 全人工时效和淬火后完全人工时效至最大硬度。
此外还有表面处理和热处理复合型的Al-Mn-Zn合金、耐磨型过共晶Al-Si合金和防爆防振型Al-Zn合金等。另外还有压铸铝合金复合材料,目 前尚未普遍生产与应用。
2 压铸件的气孔缺陷及产生原因
铝合金压铸生产的工件常因气孔存在而导致报 废,产生气孔的原因很多,在解决这一产品质量问题 时常常无从下手,如何快速、正确地采取措施减少因 气孔而造成的废品率,这是各铝合金压铸厂家所关 注的问题。
在铝合金压铸生产中,依气孔产生的原因,常有 如下几类。
2. 1 精炼除气质量不良产生的气孔
在铝合金压铸生产中,熔化了的铝液浇注温度 一般常在610~660℃,在此温度下,铝液中溶解有 大量的气体(主要是氢气),铝合金氢气的溶解度与 铝合金的温度密切相关,在660℃左右的液态铝液 中约为0.69cm3/100g,而在660℃左右的固态铝合 金中仅为0.036cm3/100g,此时液态铝液中含氢量 约为固态的 19 ~20 倍。所以当铝合金凝固时,便有 大量的氢析出以气泡的形态存在于铝合金压铸件 中。
减少铝液中的含气量,防止大量的气体在铝合 金凝固时析出而产生气孔,这就是铝合金熔炼过程 中精炼除气的目的。如果在铝液中本来就减少了气 体的含量,那么凝固时析出气体量就会减少,因而产 生的气泡也显著减少。因此,铝合金的精炼是非常 重要的工艺手段,精炼质量好,气孔必然少,精炼质 量差,气孔必然多。保证精炼质量的措施是选用良 好的精炼剂,良好的精炼剂是在660℃ 左右可以起 反应产生气泡,所产生气泡不太剧烈,而是均匀不断 的产生气泡,通过物理吸附作用,这些气泡与铝液充 分接触,吸附了铝液中的氢将其带出液面。因此冒 泡时间不宜过短,一般要有6~8min的冒泡时间。
当铝合金冷却到300℃时,氢在铝合金中的溶 解度仅为0.001cm3/100g以下,此时仅为液态时的1/700,这种凝固后氢气析出而产生的气孔是分散 的,细小的针孔,这不影响漏气和加工表面,肉眼基 本看不见。
在铝液凝固时因氢气析出所产生的气泡比较 大,多在铝液最后凝固的心部,虽然也分散,但这些 气泡常常导致渗漏,严重时常导致工件报废。
2. 2 因排气不良产生的气孔
在铝合金压铸中,因模具的排气通道不畅,模具 排气设计结构不良,压铸时型腔内的气体无法完全 顺畅排出,造成在产品某些固定部位存在气孔。这 种由模具型腔中气体形成的气孔时大时小,气孔的 内壁呈铝与空气氧化的氧化色,与氢气析出产生的 气孔不同,氢气析出气孔内壁不如空气孔光滑,没有 氧化色,而是灰亮的内壁。对于因排气不良而产生 的气孔,应改进模具的排气通道,及时清理模具排气 通道上的残留铝皮就可以避免。
2. 3 因压铸参数不当造成卷气产生的气孔
在压铸生产中压铸参数选择不当,铝液压铸充 型速度过快,使型腔中气体不能完全及时平稳的挤出型腔,而被铝液的液流卷入铝液中,因铝合金表面 快速冷却,被包在凝固的铝合金外壳中,无法排出形 成了较大的气孔。这种气孔往往在工件表面之下, 铝液进口比最后汇合处少,呈梨形或椭圆状,在最后 凝固处又多又大。对于这种气孔应调整充型速度, 使铝合金液流平稳推进,不产生高速流动而卷气。
2. 4 铝合金的缩气孔
铝合金同其它材料一样,在凝固时产生收缩,铝 合金的浇铸温度愈高,这种收缩就愈大,单一的因体 积收缩产生的气孔是存在于合金最后凝固部位,呈 不规则形状,严重时呈网状。往往在产品中,它与凝 固时因氢气析出的气孔同时存在,在氢析出气孔或 卷气孔的周围存在缩气孔,在气泡周围有伸向外部 的丝状或网状气孔。
对于这种气孔,应从浇铸温度着手解决,在压铸 工艺条件允许的情况下,尽量降低压铸时的铝液浇 铸温度。这样可以减少铸件的体积收缩,减少缩气 孔及缩松。如果常在加热部位出现这种气孔,可以 考虑增加抽芯或冷铁,使其改变最后凝固部位,解决 渗漏缺陷问题。
2. 5 因产品壁厚差过大而引起的气孔
产品形状常有壁厚差过大问题,在壁厚中心是 铝液最后凝固的地方,也是最易产生气孔的部位,这 种壁厚处的气孔是析出气孔和收缩气孔的混合体, 不是一般措施所能防止的。
对产品的形状在设计时就应考虑尽量减少壁厚 不均匀,或过厚的问题,采取空心结构,在模具设计 上应考虑增设抽芯或冷铁,或水冷,或增加模具此处 的冷却速度。在压铸生产中,要注意厚度大部位的 过冷量,适当降低浇注温度等。
从上述气孔的分类可知,在铝合金压铸生产中 产品产生气孔的原因很多,必须找出原因对症下药 才能解决问题。防止气孔的措施和途径主要有:
(1)保证铝合金熔炼的精炼除气质量,选用好 的精炼剂、除气剂,减少铝液中的含气量,及时清除 液面浮渣、泡子之类氧化物,防止再次带入气体进入 压铸件中。
(2)选择良好的脱模剂,所选用的脱模剂应是 在压铸中不产生气体的,又有良好脱模性能的。
(3)保证模具排气通畅不堵死,排气顺畅,保证 模具中的气体完全排出,尤其是在铝液最后聚合处 排气通道必须通畅。
(4)调整好压铸参数,充型速度不可过快,防止卷气。浇铸温度也要控制好。
(5)产品设计和模具设计中应注意抽芯和冷却 的使用,尽量减少壁厚差过大。
(6)对常在固定部位出现的气孔,应从模具和 设计上改善。
3 铝合金压铸技术的新发展
近年来,人们为了解决压铸件内部存在的气孔 和缩孔问题,使之能生产出高强度、高致密性、可焊 接、能进行热处理、可扭曲等各种性能的压铸件,在 继续完善真空压铸以外又发展了挤压铸造和半固态 压铸等新技术,并概括地称之为“高密度压铸法”。
3. 1 真空压铸技术
真空压铸法是将型腔中的气体抽空或部分抽 空,降低型腔中的气压,以利于充型和排除合金熔体 中的气体,使合金熔体在压力作用下充填型腔,并在 压力下凝固而获得致密的压铸件。
3. 2 充氧压铸技术
压铸件中的气体绝大部分为 N 2 和 H 2 ,几乎没 有 O 2 ,主要原因是 O 2 与活性金属发生反应生成了 固体氧化物,这为充氧压铸技术提供了理论基础。 充氧压铸是在压铸前将氧气充入型腔,取代其中的 空气。当进入型腔时,一部分氧气从排气槽排出,残 留的氧与金属液发生反应,生成弥散状的氧化物微 粒,在铸型内形成瞬间真空,从而获得无气孔的压铸 件。
3. 3 半固态压铸技术
半固态压铸是在液态金属凝固时进行搅拌,在 一定冷却速度下获得约 50% 甚至更高固相组分的 浆料,然后通过压铸使浆料成形的技术。目前,半固 态压铸有两种工艺:即流变成形工艺和触变成形工 艺。前者是将液态金属送入特殊设计的压射成形机 筒中,由螺旋装置施加剪切使其冷却成半固态浆料, 然后进行压铸。后者是将固态金属粒或碎屑送入螺 旋压射成形机中,在加热和受剪切的条件下使半固 态金属颗粒经压铸成形。
3. 4 挤压压铸技术
挤压压铸又称“液态金属模压”。其铸件致密 性好,力学性能高,且无浇冒口。我国一些企业已将 其应用于实际生产中。挤压压铸技术具有极好的工 艺优势,它不仅能替代传统的压铸、挤压铸造、低压 铸造、真空压铸工艺,还能对差压铸造、连铸连锻、半固态流变铸造工艺进行兼容。专家认为,挤压压铸 技术是一项前沿性的新技术,横跨多个工艺领域,内 涵丰富,创新性强,极具挑战性。
3. 5 电磁泵低压铸造技术
电磁泵低压铸造是一种新崛起的低压铸造工 艺,同气体式低压铸造技术相比,在加压方式方面与 其完全不同。其采用非接触式的电磁力直接作用于 液态金属,大大降低了由于压缩空气不纯及分压过 高所带来的氧化和吸气等问题,实现了铝液的平稳 输送和充型,可防止由于紊流造成的二次污染。另 外电磁泵系统完全采用计算机数字元控制,工艺执 行非常准确、重复性好,使这种工艺在成品率、力学 性能、表面质量和金属利用率等方面都具有明显优 势。随着研究的不断深入,这项工艺也愈来愈成熟。
4 结 语
铝合金圆盘、圆筒压铸件由于其壁厚不均匀,容 易产生气孔和缩气孔等压铸质量缺陷。通过不断的 浇注试验,工程师可以寻求更优化的压铸工艺参数。 这样既能选择合理的工艺参数,又能避免实际浇铸 的成本浪费,为企业带来显著的经济效益。希望通 过本课题能对实际生产有一定帮助,最终的目的是 生产出合格的压铸件,满足企业实际生产的需求。 从近年来的国内外压铸研究来看,随着理论研究方 面工作的更加深入,尤其是计算机模拟技术的发展, 使金属在填充型腔的流动形态、金属在型腔中的凝 固过程、型腔内金属液体的流动压力、模具的温度梯 度、模具的变形等方面有很大的理论突破。